テーブルソーは木材の横挽き(クロスカット)、縦挽き(リッピング)、大入れ、さね加工など木工加工の基本となる加工を行う加工機です。
日曜工作ランドでは、横挽き:クロスカットソー、縦挽き:マキタの丸鋸スタンドを使用していました。横挽きは特に不自由はありませんが、縦挽きについては作業性や仕上がりに物足りなさがありました。
資金と場所があれば、テーブルソーの購入を考えるのですが、なにせ裏庭工房では保管場所にも困ります。(お金にもっと困っていますが・・)
日曜工作ランドでは、・ローコスト・自作で・収納可能な木工加工機を手掛けてきましたので今回も自作テーブルソーにチャレンジすることにしました。
|
テーブルソーは本場アメリカでは数多くの機種が販売されています。
テーブルソーには、
・キャビネット ソー (大型)
・コントラクタースタイル ソー (中型)
・ベンチトップ ソー (大型)
の3つに分類されます。下の写真はコントラクタースタイル ソーのひとつです。このクラスの値段は$600〜$900、日本円では10万円弱ということになります。
各部の名称は下図の通り。殆どがカタカナで、耳慣れない言葉ばかりです。
|
|
本場アメリカの参考書を購入して勉強です。Fine Woodworkingニューベストシリーズ「Working with Tablesaw」\2205をオフコーポレーションで購入。内容は写真とイラストが多く、それだけでも勉強になりますが、欲張って電子辞書を片手に英文も半分程度は読みました。
この本では
・テーブルソーの基本
・良いブレードのチョイス
・キックバック対策
・各種加工テクニック
が丁寧に解説されています。
これを参考に自作プランを考えました。
|
|
■完成写真
|
|
■注意
テーブルソーはとても便利ですが、指や腕が飛んでしまう危険性があります。
また、「キックバック」により本人どころか、近くにいる人に危害を加える(場合によっては命に関わる)可能性があることを、十分に理解の上、取組んでください。
かく言う私もこの教科書により、その危険性を再認識した次第です。
|
|
■テーブルベース
|
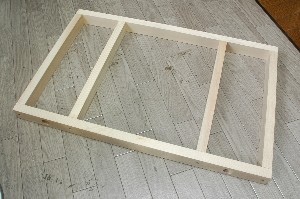
|
日曜工作ランド式万能加工台の使用を前提としてのテーブルベースを作成します。
サイズをどうするか迷いました。大きい方が便利だが、収納に困る。そこでミニマムサイズとしてW700xD450にしました。
巾方向700ミリ:最大30センチまでカットできること。それから加工の汎用性を持たせる為に左右対称とし、ブレードを中央に配置。
奥行き方向450ミリ:日曜工作ランド式万能加工台の奥行きが約500ミリなので一回り小さく。
この大きさでは長いものをカットする場合は向こう側に材料が落っこちてしまいます。アウトフィードテーブル(延長テーブル)を後付けする構想にしました。
骨組みの材料をホームセンターに探しに行ったところ、24ミリx45ミリの米栂集成材がありましたので購入してきました。天板は12ミリの合板を使用。
|
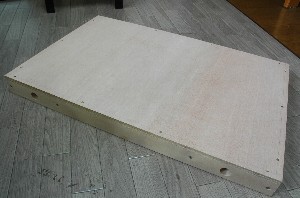
|
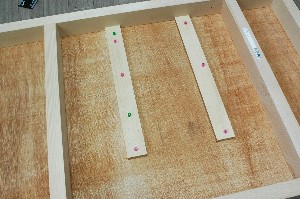
|
電動マルノコには加工時に力が加わるので、ズレ止めの合板を取付ます。(接着剤を塗って乾くまで仮釘で固定)
|
|
|
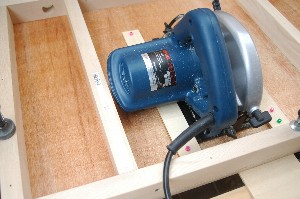
|
電動マルノコのモーターの部分が骨組みと干渉することが分かったので干渉しない位置まで骨組みを移動しました。 |
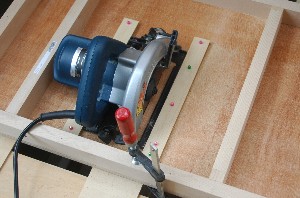
|
鋸刃を完全に引っ込めた状態でマルノコベースをズレ止め合板にあてがい、天板にゆっくりと鋸目を入れます。
|
|
|
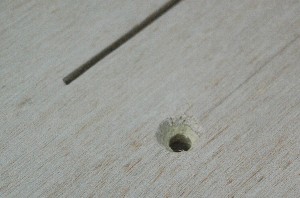
|
マルノコの固定には6ミリの皿頭ネジを使用します。
ビス頭が飛び出さないように皿穴加工をします。
皿穴加工には面取りカッターを使用。なぜか、軸がぶれて多角形っぽい皿穴になってしまいました。
|
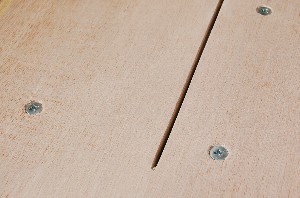
|
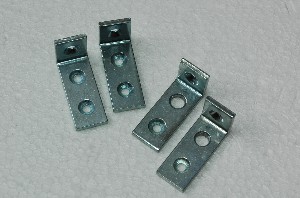
|
続いて、固定金具の作成。マルノコのベースに返しが付いているのでコの字型の金具を作る必要があります。
金折れ(L型アングル)の穴をドリルで6ミリに広げます。(上写真)
その後、端をバイスでつかんでおいてハンマーで叩いてコの字型に曲げます。
下の写真のようにズレ止め合板部分に使用しますのでコの字は非対称形にします。
|
|
|
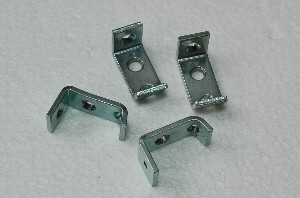
|
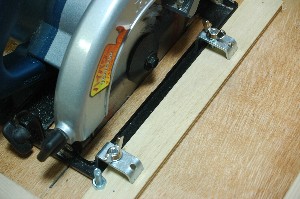
|
コの字型金具を用いての固定状況。
固定には蝶ナットを使用。
|
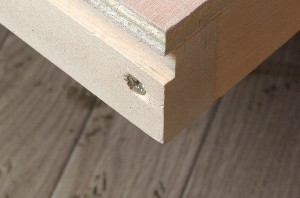
|
後から思い立って、フェンスのランナーを走らせる為の溝を加えました。
|
|
|
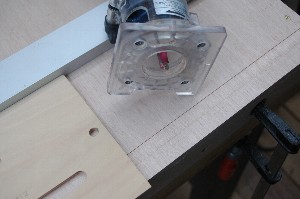
|
メジャーテープ用に深さ0.5ミリの溝を切ります。毛羽立ちが激しかったのでカッターで切れ目を入れてから加工しました。
|
|
|
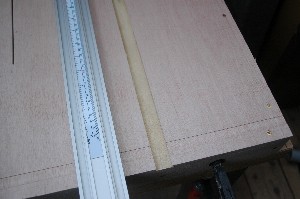
|
メジャーテープ用の溝とは直交方向にマイターゲージスロット(溝)をトリマーで掘ります。加工にはシステムバークランプを使用しました。
このスロット(溝)を利用して、クロスカットスレッドも作る予定です。
※「マイターゲージ」や「クロスカットスレッド」については後程紹介します。
ランナーには5ミリx20ミリのアルミフラットバー(ホームセンターで調達)を使用することのしました。フラットバーの幅が20ミリですが、スムーズに滑らせる為にはスロット(溝)の幅を20.5ミリにしました。
|
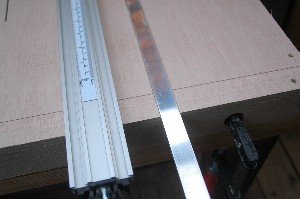
|
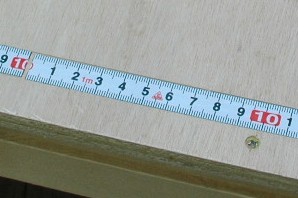
|
切って貼れるメジャーテープを貼付。目盛りでカット寸法が決まるように貼り付けました。
|
|
|
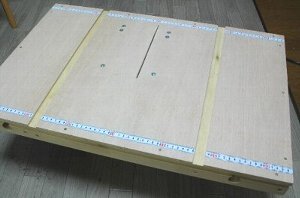
|
これで、ベース部分が完成しました
※電動丸鋸を止めるボルトが6本あるのは、穴の開け間違い!穴が開いたままなのもカッコ悪いので、穴隠し用にボルト締めしています。
|
|
■フェンス
|
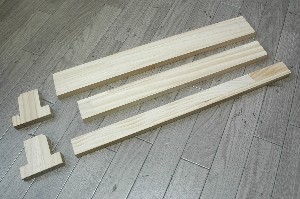
|
フェンスには、18mm厚のパイン集成材を使用。
フェンスは断面をカタカナのコの字型にしてかなり頑丈な構造にしています。(ちょっと過剰でした。)
|
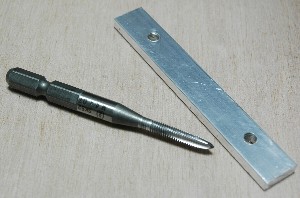 |
フェンスのランナーとして4ミリx12ミリのアルミフラットバーを使用。
アルミフラットバーに3.3ミリの下穴をあけたあと、M4の タップを切ります。
|
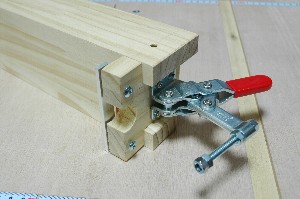
|
フェンスの固定に何を使うかさんざん悩んだ結果、ワンタッチで固定できるようにと、トグルクランプ(GoodHand
GH11421)を使用することにしました。(Amazonでも扱っています)
トグルクランプは左上の状態から左下の状態にすることでワンタッチでボルトの先端部分で圧締します。
強い圧締力がボルト部に集中し、木材が凹んでしまいそうでしたのでアルミのフラットバーを噛ませることにしました。
アルミのフラットバーは木材に対してルーズにすることによってトグルクランプの力をうまくテーブルベースに伝えられるように工夫しました。
(木材の穴は4.5ミリ、フラットバー固定ビスは4ミリ)
ボルトは長さが合わなかったので寸切りボルトを使用しています。
|
|
|
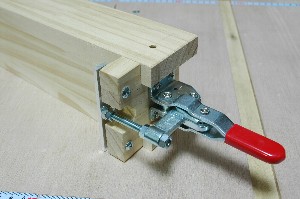 |
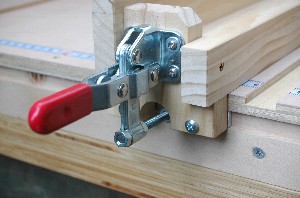 |
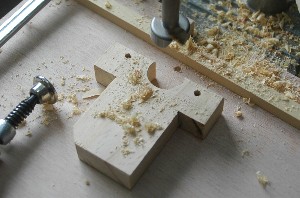
|
説明が前後しますが、トグルクランプの圧締ボルトの部分はフォスナービットで切り欠きました。
|
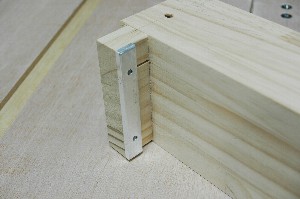 |
反対側は4ミリx12ミリのアルミフラットバーにM4のタップを切ってビスで固定します。
|
|
|
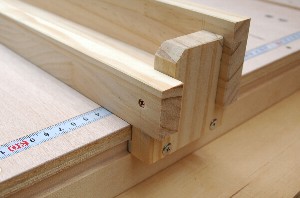 |
テーブルベースに取付けたところ
|
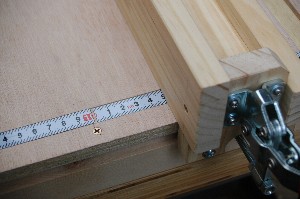 |
カット寸法はフェンスの位置をメジャーテープに合せることでダイレクトに寸法が決められます。
鋸刃との平行を確保する為に、奥と手前の2つのメジャーテープの寸法を合わせます。
|
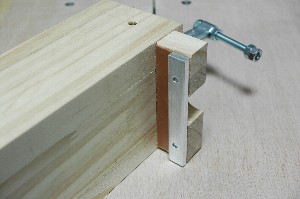 |
フェンスのすべりが悪く(ガタツキもあり)うまく左右に動いてくれません。そこで敷居スベリを貼り付けたところ、なんとか使用に耐えれる状態になりました。
敷居スベリは滑りが良い反面、フェンスの固定部に使うと、力が加わるとずれる懸念があります。
なので、トグルクランプ側につけました。こうすれば、圧締時点では接触しなくなるので解決です。
|
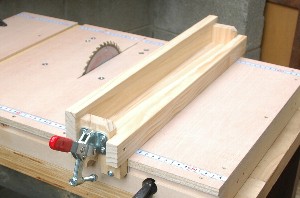 |
装着写真
|
|
■集塵カバー
|
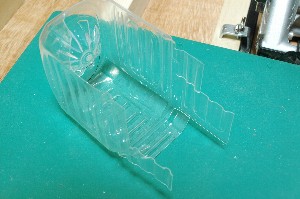
|
試しカットをしてみましたが、かなりの鋸くずが舞い上がります。
PETボトルを使って集塵カバーの製作です。あまり凝ったことは考えず、なるべく集塵効率が高くなるようにと考えました。
今回はアクエリアスの1リットル容器を使用。
|
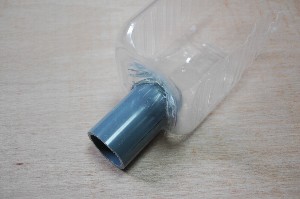 |
38ミリ ダクトホースに相性が良いVP30の塩ビパイプを適当な長さにカットして埋め込みます。
PETボトルの底は肉厚がごつく穴あけに苦労しました。(小径のドリルとハンドルーターを駆使して穴開け)
塩ビパイプの接着には裏から雨樋用接着剤、表から3Mプラスチック用接着剤で固定。
|
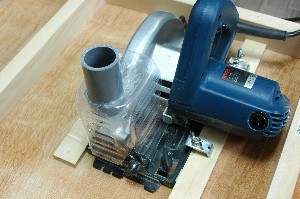 |
装着後の写真。結構いい感じです。
難点は、刃高の上げ下げに追従できない点。刃高いっぱいでのセッティングに合わせていますので刃を低くしたいときは、集塵カバーを外す必要があります。
|
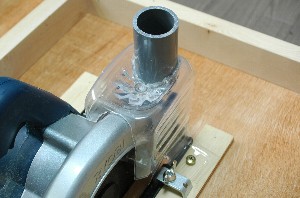 |
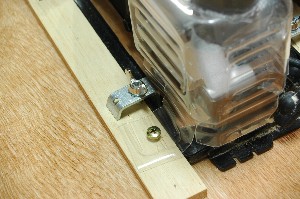 |
集塵カバーの固定。PETボトル固定用のタブを残しておいて固定します。
一方はビス固定。
|
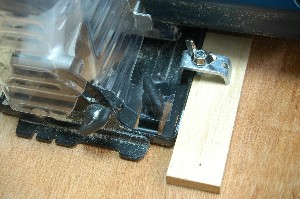 |
一方のタブは平行ガイド取付用の蝶ネジを使用して固定。(写真中央の黒いつまみ) |
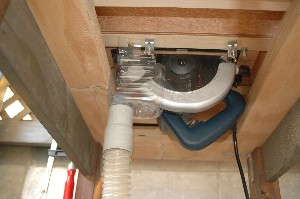 |
捕集率は50%くらい?無いよりましといったレベル。カバーの中に鋸くずがたまる始末。今後改良の余地ありです。
|
|
|
|
|
■プッシュスティックとプッシュブロック(安全対策その1) |
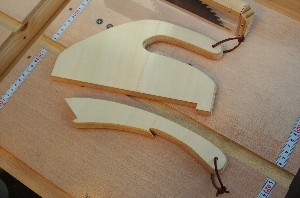
|
テーブルソーには必須のプッシュスティックとプッシュスブロックを作ってみました。
|
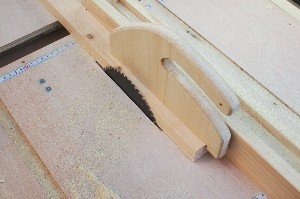 |
特に、巾が狭い材料をカットする時に、ブレードの近くに手をやらくて済むので安全が確保できます。
|
|
■スプリッター(安全対策その2) |
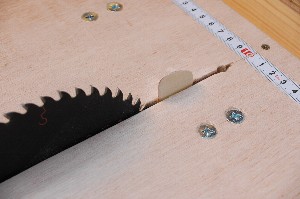
|
ブレードの延長線上に付ける「スプリッター」。「キックバック」を防ぐ上で最も有効な対策です。
スプリッター材料には模型用に販売されている”航空ベニア(1.5ミリ)”を使用しました。
チップソーの厚みは1.6ミリ。スプリッターの厚みも同じ位にすべきですが、取付が難しいので1.3ミリ程度まで削りました。
※正確にブレードの延長線上に接着するのは結構難しく1度付けた後でやり直しました。
|
|
「キックバック」とは材料をカットする際、材料の角がブレードに引っ掛かって持ち上げられ、後方に飛ばされていく現象です。
「キックバック」を防止する上で、材料をフェンスに押し付ける力を加え続けることがとても重要です。
「スプリッター」は、「キックバック」を防ぎます。
|
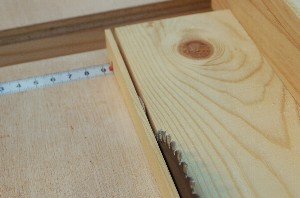
|
加工状況。スプリッターがあれば、加工直後の材料がブレードに巻き込まれる危険が少なくなります。
|
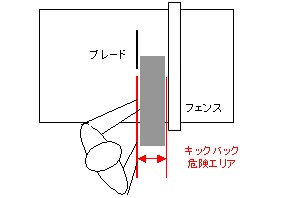
|
ここで、フェンスはブレードの右側か左側について紹介します。
イラストのように、材料の後がキックバックの危険エリアとなります。
右利きの場合、右手で材料をフェンスに押し付ける力を加えながら送る為には、右のイラストのようにフェンスをブレードの右側に配置して作業するのが自然で、かつ危険エリアを避けることができます。
※マキタの丸鋸スタンドは反対ですね。
|
|
■ブレードカバー(安全対策その3)
|
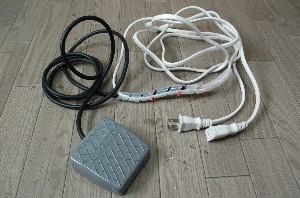
|
電動丸鋸本体のスイッチは入れっぱなし(ホールド)にしておき、フットスイッチでON/OFFをしています。(踏むとON/離すとOFF)
とても便利ですが、誤ってスイッチが入る可能性が高く、そのままではとても危険。
|

|
ひとつは、元スイッチを用い、作業が終わるごとに元スイッチを切るようにします。
(でも時々忘れてしまう・・)
|
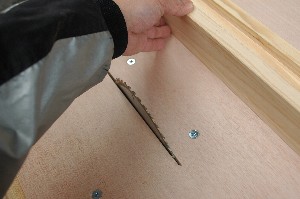
|
危険!
作業の合間ではありますが、フェンスのセットを両手で行う関係上、写真のように左手がブレードをかすめます。
万が一、ここでスイッチが入ってしまったらと考えるだけでも恐ろしいです。
|
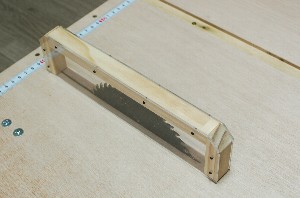
|
そこで、単純に、「加工時以外はカバーをする」ことを考えました。これで、加工時以外に誤ってスイッチが入ってしまった場合の安全性が確保できます。
※加工時以外は常にカバーをしておくという原則のもとで・・
|
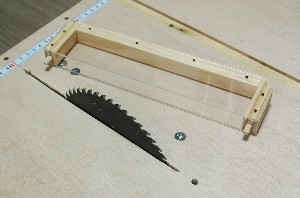
|
材料は2ミリのアクリル板と18ミリ集成材の端材。6ミリの木ダボを用いて脱着可能な構造にしています。
|
|
|
|
■アウトフィードテーブル |
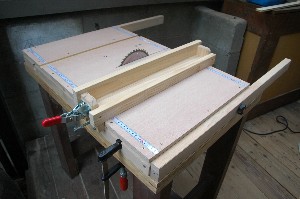
|
本体の両サイドに腕を付けてアウトフィードテーブル(延長テーブル)を支えようという考えです。
写真は仮組みの状態
|
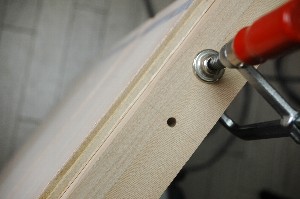 |
腕の固定穴。
腕の穴と、本体に開ける穴(2点支持)をぴったりに開けること難しい(というか、微妙にずれてしまうことが多く、うまく出来ません)ので予め腕の方に貫通穴を開けておき、その穴をなぞってドリルで本体に穴を開けることで完全に同じ位置に穴を開けることが出来ます。
|
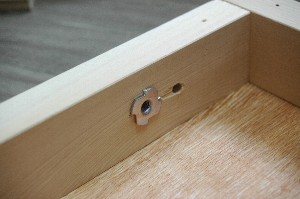
|
開けた穴の裏側をリーマーで広げて爪付きナットを埋め込み。※ 奥の穴は開け間違い!
|
|
|
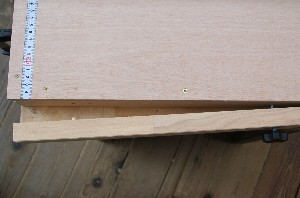 |
取付を簡単にする為に、1点(写真左)は木ダボ、1点(写真右)はボルトにノブスターを付けて取付にしました。
( 当然ですが、木ダボは接着せずに抜き差しできる状態です)
我ながらグッドアイデア!
|
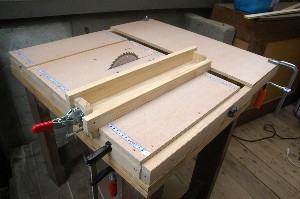
|
ここでアウトフィードテーブルの板を仮置きして試し切りしてみました。
これは便利・・というか、常に必要です。
ここで、方針変更!!
アウトフィードテーブルは脱着せずに付けたままにすることにしました。
元々は分解して収納することを考えていましたが、付けたままで収納できるように、収納側を工夫することにしました。
|
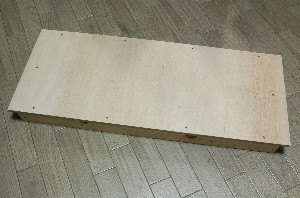 |
テーブル部分。本体と同じく、骨組みに合板を貼って作ります。(ちょっとごつ過ぎた!)
|
|
|
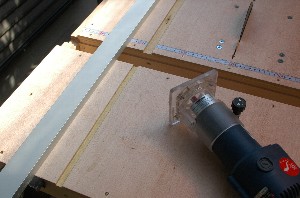
|
マイターゲージスロット(溝)を本体の延長線上にも加工します。写真はケガキしているところ。
左右2本のスロットが完全に平行になるように注意深く加工します。
|
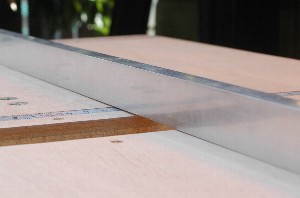 |
水平の確認。
定規(アルミ角パイプ)をあてがうとアウトフィードテーブル(手前)の方が高くなってしましました。これでは加工時に材料がつっかえてしまいます。
腕木を削って高さを揃えました。(正確にはアウトフィードテーブルのほうを若干低くしました)
|
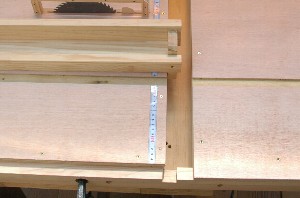 |
腕木にはフェンスが干渉しますので一部切り欠きを加えました。
腕木は、先に紹介したノブスターは取り止めて普通にボルト締め。
|
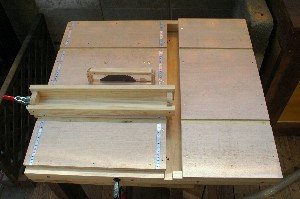 |
アウトフィードテーブルが取り付き、これで完成です。
※あとの祭りですが、 最初からアウトフィードテーブル一体の設計にすれば良かったです。
|
|
■作業台に取付け |
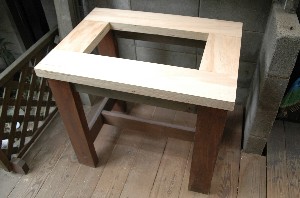 |
日曜工作ランド式 万能作業台
中央に開いた穴の部分に電動丸鋸本体を落とし込みます。
|
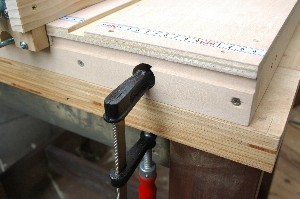 |
予め開けておいた穴を利用してクランプで固定します。
|
|
|
|
■図面ダウンロード |
<本体>
|
|
←図面のダウンロード
はこちら。
(PDFファイル)
|
|
<フェンス>
|
|
<アウトフィード テーブル>
3/21追加
|
|
<クロスカット スレッド>
3/21追加
|
|
ご自由にダウンロードして頂いて結構ですが、著作権は放棄していませんので無断転載・再配布・販売はしないで下さい。
|
|
|
|